Benefits of modular construction for social landlords
Modular construction is a method of building that involves manufacturing prefabricated modules in a controlled factory environment before transporting them to site for assembly. This method of construction has a number of advantages over traditional construction methods, particularly within the social housing market.
Connect Modular, part of the Ayrshire based Wee House Group, specialise in modular construction and producing houses that are 90% complete, with kitchens, bathrooms, plumbing and electrics installed and quality checked before leaving their factory in Cumnock, East Ayrshire. Under most contracts Connect Modular takes on the Principal Contractor role, managing all aspects of the project from design and statutory consents to manufacture of housing and construction of ground and site works. This ensures a single point of responsibility for affordable housing clients.
Quality
The main benefit of modular construction is the standard of product that is achieved. Quality is at the heart of this family run business and is assured by independent, BOPAS accreditation. The controlled factory environment facilitates a stringent quality regime, resulting in high standards of finish and performance. A ‘right first time’ policy and ‘zero defects’ ethos is adopted by Connect Modular and embedded through ISO9001-aligned quality assurance procedures in manufacturing and construction processes. The manufacturing process also delivers a safer method of construction, improving health and safety for the workforce and communities within which new housing projects are located.
Organisational culture is just as important as accredited processes and Connect Modular encourages staff to take pride in the quality of their craft, to be open and work collaboratively. The quality of Connect Modular’s product is monitored internally by a Factory Floor Manager and Quality Manager whilst the company’s Technical Manager and Production Manager are based in the factory and therefore available to resolve any technical queries or issues that arise. The factory operates an open door policy for client representatives, Clerk of Works and Quantity Surveyors with the value of inspection improved through the cleaner, more organised and accessible environment in comparison to a traditional building site.
Modules can be delivered to site, craned into position, fixed together and made wind and watertight on the same day. This process vastly diminishes the potential for moisture ingress and becoming trapped in the structure, thereby reducing the risk of shrinkage. All timber is FSC sourced and moisture checked in the factory before use. Furthermore, with building materials stored in a dry, undercover setting, the risk of damage and resultant waste is reduced significantly. Any materials required to finish houses on site are delivered within the modules themselves, minimising waste and protecting from damage. This all leads to less risk of defects than with traditional construction methods.
Programme
One of the main advantages of modular construction is that it is faster and more predictable than traditional construction methods. Working in a controlled environment means superstructure construction is not subject to the same delays and disruptions traditional approaches are exposed to, a particular advantage in the Scottish climate. Groundworks take place at the same time as module manufacturing, compressing programmes and delivering much needed affordable housing more efficiently.
Connect Modular seeks to support local economies as far as possible with the remaining 10% of work completed on-site and the associated service requirements. The homes can be completed in a matter of weeks, ensuring quick occupancy for residents who are in need of affordable housing and earlier realisation of rental income and loan repayment for clients.
Sustainability
Another advantage of modular construction is that it is more sustainable than traditional construction methods; better air tightness can be achieved as standard, material off-cuts are sorted and re-used more readily, recycling and general waste can be more efficiently segregated, and even cardboard and plastic packaging is kept dry prior to bailing and recycling. Bulk deliveries to the factory and reduced time on-site minimises construction traffic and related emissions by up to 50%, all of which leads to quieter and less disruptive impacts on local communities and businesses.
Connect Modular can deliver to a client’s preferred energy standards with a high performing fabric further enhanced by renewable technologies including Air Source Heat Pumps and Photovoltaic panels.
Connect Modular have a number of completed and ongoing projects in the social housing market, including having recently completed Scotland’s first large-scale modular housing development, for Riverside Scotland, a 63 unit scheme in Dundonald, South Ayrshire. They are currently delivering 101 modular affordable homes for Cunninghame Housing Association in Shortlees, Kilmarnock; six amenity bungalows for North Ayrshire Council in Stevenston; and 21 amenity blocks on a site for travelling people for Aberdeen City Council.
Connect Modular is committed to providing high-quality, affordable housing that meets the needs of both their clients and end-users occupying the homes. They believe that modular construction is a sustainable and efficient way to build homes and are proud to be a pioneer in the affordable housing market.
Connect Modular is one of twenty companies that have been appointed to our H2 New Build Housing Construction framework that launched in August last year. The H2 framework offers a range of traditional housing, as well as low, medium, and high-rise construction, care homes, mixed-use sites, student and keyworker accommodations with an intrinsic focus on creating net zero buildings. In addition, associated civil engineering and infrastructure works are covered by the framework.
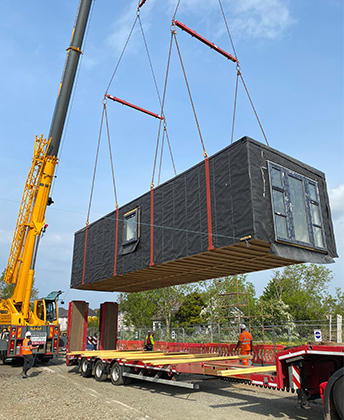